Damage prevention case 1
I want to prevent the cracking of a hole near the edge during heat treatment. (S45C-D)
There are several methods to choose from.
After studying the usage, we proposed to change the fabrication sequence and the heat treatment method, and solved the problem.
Damage prevention case 2
TD processed threaded parts had broken.
Considering their function, the material could be changed safely from SKD11 to tougher SKD61. This change improved the yield ratio.
Damage prevention case 3
I want to harden the surface of gears uniformly, but only the tooth part gets hardened and break.
For example, with induction hardening, we can select the optimized frequency from low, middle and high frequencies.
In this case, we selected frequencies to harden the gears uniformly. Please consult us.
High frequency: quickly heats up a thin surface
Medium frequency: in the middle between high and low frequencies
Low frequency: slowly heats up into a deeper surface
Damage prevention case 4
I am carburizing bearings but galling defects are showing up.
A certain bearing manufacturer (A) asked us about this problem.
These carburized bearings were used for automobile rotating seats. A further investigation on their usage revealed that an excessive frictional force was applied to a sliding part to cause plastic deformation, which in turn caused galling.
At Metal Heat Treatment Solution, we have proposed nitriding (gas soft nitriding) method, which is more wear resistant than carburizing, to solve the problem.
Damage prevention case 5
When induction hardened S45C is bored through, the edge gets chipped.
We solved the problem by proposing a different material and heat treatment method.
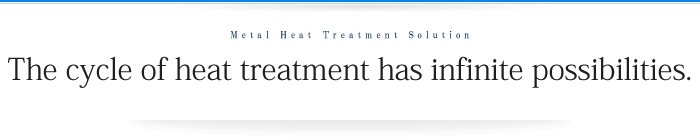

For details of equipment specifications, please refer to the "Equipment" section in "Heat Treatment technology of the Solution" page.
Heat treatment method
We own various equipment including vacuum heat treatment, salt bath heat treatment, carburizing heat treatment, induction hardening, nitriding heat treatment, etc.
We also own various testing instruments, such as sub-zero equipment, various hardness testers, metallographic examination equipment and coercive force meters.