Shorter delivery time case 1
Please start processing as soon as possible because processing a single item order with gas carburizing usually takes a long time.
We can flexibly deal with orders with short delivery time because we own an open type furnace (liquid carburizing furnace), which, unlike a gas furnace, is suited to treat single item orders.
For example, in case of carburizing a layer to 0.8 mm, there is no big difference in processing time of a gas furnace and a liquid carburizing furnace.
While an open type furnace can start treating a piece at any point, however, the same piece needs to wait before being treated in a gas furnace. We can flexibly treat various thicknesses of carburized layer upon request from customers. For example, a carburized layer of 0.3 mm takes only 5 hours at fastest.
Shorter delivery time case 2
I don't have time!
Although it really depends on the materials and heat treatment method, we will do our best.
As for a reference, our record speeds of various types of treatment are shown below.
Vacuum quenching: 6 hours
Salt bath quenching: 2 hours
Gas carburizing: 12 hours (carburized layer 0.6 mm in thickness without shot blasting)
Gas carburizing with anti-carburization: 24 hours (carburized layer 0.6 mm in thickness without shot blasting)
Liquid carbonitriding: 5 hours (carburized layer thickness of 0.3 mm)
Gas soft nitriding: 5 hours
Induction hardening: 10 minutes (4 hours with tempering)
'* The treatment time changes depending on the material and heat treatment method.
In any case, a meeting in advance is necessary.
Shorter delivery time case 3
I want to omit the sub-zero treatment and shorten the delivery time without compromising the quality.
This was a case of carburizing SNCM. By controlling the carbon potential (CP) at the carburizing stage, it was possible to maintain the quality as high (to reduce retained austenite as much) as the case of sub-zero treatment after carburizing. As a result, we could shorten the delivery by omitting sub-zero treatment.
Conventional method: quenching → sub-zero → tempering
Solution method: quenching (CP adjustment) → tempering
Shorter delivery time case 4
Long shafts have strong distortion and they are increasing the workload in the latter process.
The customer had been carburizing shafts (Ф50 x 670) in a batch furnace, but had distortion of over 1 mm. The requirement was to create a carburized layer thick enough to allow polishing afterwards, but that created problems of delivery, cost and low workability at the latter process. We changed the furnace to a pit type to treat them vertically and also changed the cooling method to a salt bath method in order to suppress the distortion of the long piece. In addition, we have reviewed the ways to set the shafts on jigs and successfully reduced the distortion to 0.3 mm.
By reducing the distortion from 1 mm to 0.3 mm, we could also reduce the steps in the polishing process and carburizing time.
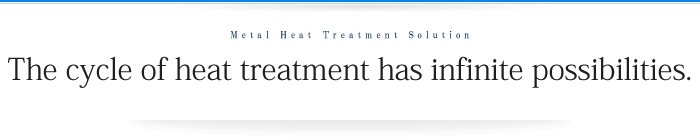

For details of equipment specifications, please refer to the "Equipment" section in "Heat Treatment technology of the Solution" page.
Heat treatment method
We own various equipment including vacuum heat treatment, salt bath heat treatment, carburizing heat treatment, induction hardening, nitriding heat treatment, etc.
We also own various testing instruments, such as sub-zero equipment, various hardness testers, metallographic examination equipment and coercive force meters.