Improved life span case 1
Can low-carbon steel achieve the hardness of HRC55 and above?
Yes, we can even process the ones with complicated shapes that inhibit the induction hardening. We will propose the optimized heat treatment method based on the usage. For example, S45C can achieve HRC60 hardness.
Improved life span case 2
Can rolled steel for general structure achieve the hardness of HRC55 and above?
Yes, even the steel with low carbon content can achieve surface hardness. We optimize the heat treatment method based on its usage, so even rolled steel for general structure can achieve the maximum hardness of HRC55 and above.
Improved life span case 3
I want to improve the wear resistance and durability of S45C by quenching entirely.
In this case, we improved the wear resistance and durability by changing the oil quenching process to salt bath quenching. Hardness improved from HRC40 - 45 to HRC55 - 60.
We will make an optimized proposal from various methods. So, please contact us.
Improved life span case 4
I want to extend the life span of molds.
Vacuum marquenching treatment can extend life span of molds by 20% and more.
We have advanced vacuum marquenching treatment into RV treatment, which aims to achieve a uniform distribution of hardness, reduced distortion and improved life span.
The conventional cooling method with compressed nitrogen gas had various problems like uneven hardness and distortion/deformation due to insufficient cooling of large molds. Our vacuum marquenching treatment (RV treatment) treats all processes in a vacuum environment from the moment products enter the furnace until the end of heat treatment and cooling. This treatment has enabled uniform distribution of hardness, reduction of distortion, and improved life span for molds. It is most effective for large hot work die steels (SKD-61, etc.) which are products that are usually used for die casting dies and various forging dies.
* Effective size: H 600 mm x W 600 mm x L 1,050 mm
Improved life span case 5
S55C doesn't harden enough with vacuum quenching.
With vacuum oil quenching, the shafts of Ф30 x 300 in size could only achieve the hardness of HRC25. The product had to be hardened to its core this time, so we chose salt bath quenching. We could raise the internal hardness using specially made salt solution.Metal Heat Treatment Solution will propose the best method out of every possible treatment.
Improved life span case 6
I am carburizing bearings but galling defects are showing up.
A certain bearing manufacturer (A) asked us about this problem.
These carburized bearings were used for automobile rotating seats. A further investigation on their usage revealed that an excessive frictional force was applied to a sliding part to cause plastic deformation, which in turn caused galling.
At Metal Heat Treatment Solution, we proposed a nitriding (gas soft nitriding) method, which is more wear resistant than carburizing and has very little dimensional change, and successfully solved the problem.
Improved life span case 7
I am nitriding bearings but they don't last long.
A certain bearing manufacturer (B) asked us about this problem. This manufacturer was nitriding bearings, but the thin nitrided hardened layer could not endure the strong pressure applied on the surface. As a result, the product had quality problems like dents. At Metal Heat Treatment Solution, we proposed carburizing and carbonitriding to create a deeper hardened layer, and successfully solved the problem.
Improved life span case 8
I want to eliminate the distortion and dimensional instability.
A certain shaft manufacturer requested us to eliminate the distortion of shafts Ф28 x 400 (S55C).In this case, we had to suppress the distortion at quenching so as not to cause dimensional instability by correcting distortion after quenching.
Correcting distortion after heat treatment causes stress, which in turn causes dimensional instability.Therefore, it becomes essential to suppress the distortion at quenching, i.e. to decrease the retained austenite amount. Several methods help decrease the retained austenite amount.
1. Adjusting carbon potential at quenching
2. Performing sub-zero treatment after quenching
3. Super sub-zero treatment is more effective
We have achieved distortion of less than 0.02 mm at quenching by arranging materials and suppressing distortion during induction hardening.
We strive for correction-free treatment by setting products vertically even for long pieces and using such equipment and know-how to cool in a salt bath.We can also examine for a retained austenite amount.
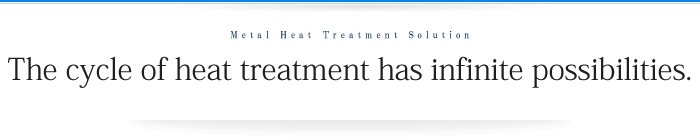

For details of equipment specifications, please refer to the "Equipment" section in "Heat Treatment technology of the Solution" page.
Heat treatment method
We own various equipment including vacuum heat treatment, salt bath heat treatment, carburizing heat treatment, induction hardening, nitriding heat treatment, etc.
We also own various testing instruments, such as sub-zero equipment, various hardness testers, metallographic examination equipment and coercive force meters.